Police Preferred Specification Explained
It is important for buildings of all types to be physically secure to deter criminal activity and reduce crime. SBD has worked with manufacturers, the construction industry and standards authorities for many years to ensure that security standards are current and updated to keep pace with emerging crime trends.
Today, SBD has more than 700 member companies with thousands of products that have achieved our Police Preferred Specification.
Our membership recognises that products not only have been tested to relevant security standards but also fully certified by an independent third-party certification body accredited by the United Kingdom Accreditation Service (UKAS).
Independent certification involves both initial testing of the products and regular re-tests as well as inspections of the manufacturer’s production facility to ensure the correct processes are maintained constantly over time to provide a more secure and reliable product. This goes beyond the level of security called for within Part Q of the Building Regulations in England 2010, which became effective in October 2015.
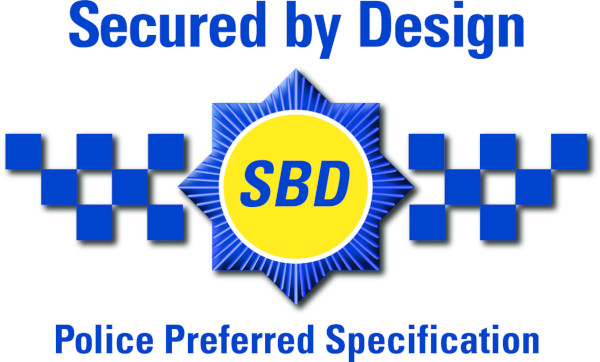
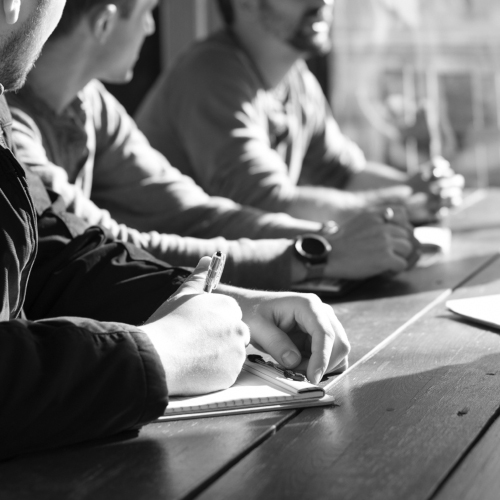
Benefits to Members
Companies that achieve our Police Preferred Specification can become an SBD member company and use our coveted logo for sales and marketing purposes. Police forces can recommend SBD accredited products and signpost members of the public to the list of SBD member companies and products.
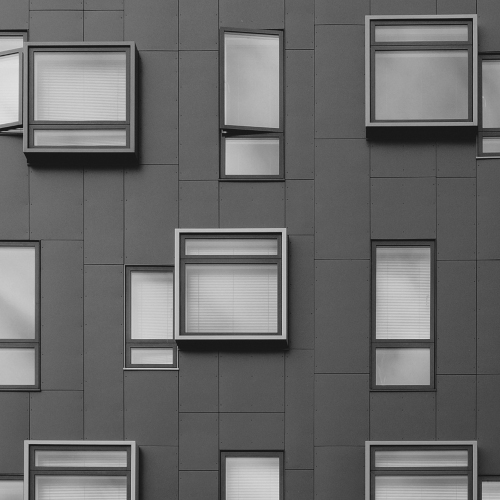
Benefits to Local Communities
Academic research has shown repeatedly over the last ten years that this requirement for SBD accredited attack resistant quality products has reduced burglary where they have been installed.
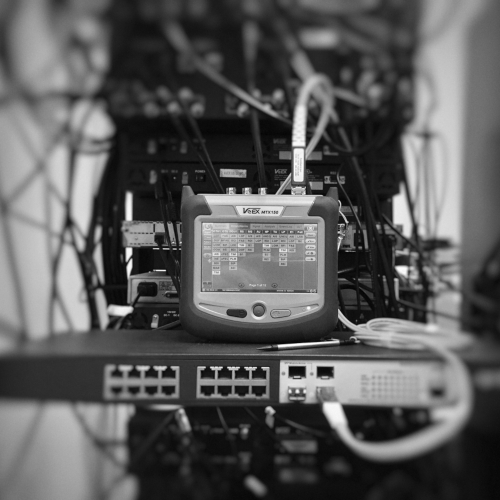
Tested Products
A manufacturer can submit a product for testing to a recognised security standard at a test laboratory, often accredited by UKAS, and pass. However, this does not ensure that the product tested is the same as the mainstream manufactured item nor is representative of the range of products.
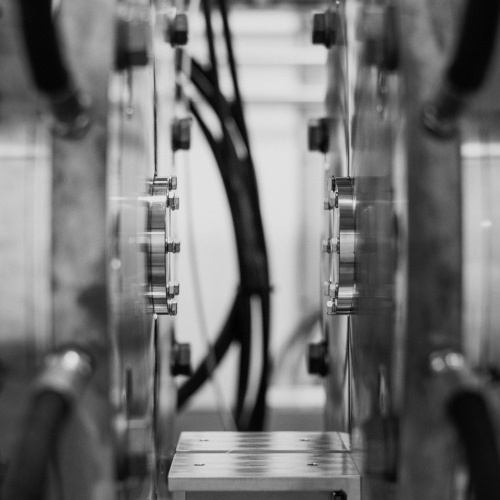
Certified Products
Certification gives quality assurance. When a manufacturer wishes to comply with the requirements of SBD they must now submit the product range for certification. This involves submission to a test house, which may or may not be the Certification Authority (CA).
A number of products, representing the whole range, are selected for testing and if they all pass they can be accepted into the certification scheme. The CA visits the production facility to ensure that the products tested are representative of the products supplied to the end user. This is followed by a programme of regular visits to ensure continued quality standards are met and that components have not been altered without informing the CA.
During the course of a year, the CA will remove a small number of products for re-testing. This is dependent on the number of products being produced or a number agreed with the manufacturer. Should any part of the security standard be changed/up-dated the manufacturer is expected to upgrade products to retain certification.